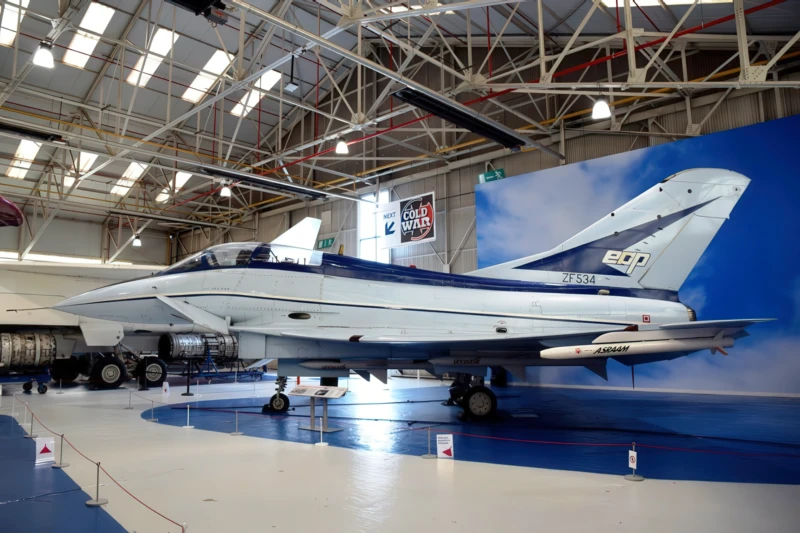
British Aerospace EAP |
|
País | Reino unido |
Tipo | Private venture demonstrator fighter |
Primeiro voo | 8 August 1986 |
Construído | 1 |
O British Aerospace EAP (standing for Experimental Aircraft Programme) is a British technology demonstrator aircraft developed by aviation company British Aerospace (BAe) as a private venture. It was designed to research technologies to be used for a future European combat aircraft, and for the multinational Eurofighter Typhoon.
Fonte: British Aerospace EAP Hawk on Wiki
BAe EAP (experimental aircraft program) Walk Around | |
---|---|
Fotógrafo | Meindert de Vreeze |
Localização | Salinas Air Show |
Fotos | 42 |
Wait, Searching British Aerospace EAP photos for you…


Veja também:
The British Aerospace Experimental Aircraft Programme (EAP): A Precursor to Modern Combat Aviation
Executive Summary
The British Aerospace Experimental Aircraft Programme (EAP) represents a seminal achievement in aerospace engineering, serving as a dedicated technology demonstrator that profoundly influenced the trajectory of modern combat aircraft development. Conceived in the early 1980s as a private venture by British Aerospace, with initial aspirations for broader European collaboration, the EAP ultimately became a predominantly UK-funded initiative. Its core purpose was to rigorously test and validate pioneering technologies deemed essential for a future advanced fighter aircraft. The EAP’s design was revolutionary for its era, characterized by inherent aerodynamic instability, sophisticated fly-by-wire flight controls, and extensive application of advanced composite materials. This combination positioned it as arguably the most advanced fighter aircraft of its time. Through a highly intensive and strategically managed flight test program, the EAP successfully demonstrated critical concepts in aerodynamics, flight control, avionics, and structural engineering. This rigorous experimentation proved instrumental in de-risking and accelerating the development of the multinational Eurofighter Typhoon, leading to significant savings in both time and financial resources. The EAP stands as a testament to visionary aerospace engineering, its enduring legacy evident in the fundamental design principles and capabilities of contemporary high-performance military aircraft.1. Introduction: The Genesis of a Game-Changer
The British Aerospace Experimental Aircraft Programme (EAP), often referred to simply as the EAP, was explicitly designed as a “technology demonstrator” and a “one-off research aircraft”. Its primary objective was to test pioneering technologies intended for an advanced fighter aircraft, underscoring its role as a dedicated testbed for innovation rather than a direct prototype for production. Developed by British Aerospace (BAe) in the 1980s as a private venture, the EAP was widely regarded as “the most advanced fighter aircraft ever built” at the time of its construction. It integrated “technologies never seen before” that positioned it significantly “ahead of its time,” reflecting its ambitious scope and the considerable leap in aerospace capabilities it represented. The EAP’s conceptual framework was deeply rooted in the earlier “Agile Combat Aircraft (ACA)” program, a collaborative initiative that commenced in the late 1970s and early 1980s. This collaborative effort initially involved British Aerospace, the West German manufacturer Messerschmitt-Bölkow-Blohm (MBB), and the Italian company Aeritalia. The multinational approach aimed to pool resources and expertise, recognizing the strategic benefits of shared technologies and development costs for a complex undertaking like a new generation of fighter aircraft for Western European air forces. A mockup of the ACA was publicly exhibited at the 1982 Farnborough Airshow and the 1983 Paris Air Show, generating international interest and showcasing the program’s progress. It was at the 1983 Paris Air Show that the official launch of the Experimental Aircraft Programme (EAP) was announced, with the initial intention to produce and fly a pair of technology demonstrators to validate these cutting-edge concepts. The EAP was specifically designed to research technologies for a “future European combat aircraft,” directly paving the way for the multinational Eurofighter Typhoon. From a United Kingdom perspective, the impetus for developing such an advanced fighter stemmed from the retirement of the English Electric Lightning, which left the Royal Air Force (RAF) without a domestically designed and manufactured agile air superiority fighter. The EAP served as a crucial instrument for mitigating programmatic risk. The high degree of cutting-edge technologies involved in developing a new generation of combat aircraft necessitated a proactive approach to reduce potential failures or unforeseen challenges. By isolating and testing revolutionary elements, such as inherently unstable aerodynamic configurations and full-authority digital fly-by-wire systems, on a dedicated, single-platform demonstrator, potential issues could be identified and resolved in a controlled environment. This foresight in de-risking was essential for the viability and eventual success of the much larger, multi-national Eurofighter program, preventing costly delays and redesigns in later, more expensive production stages. Furthermore, the EAP acted as a catalyst for European aerospace collaboration, even amidst initial funding shifts. While the program was initially intended as a tripartite partnership, West Germany’s subsequent decision not to provide funding led to the cancellation of the planned second EAP airframe, and the program became predominantly funded by the UK. However, the initial intent for collaboration was driven by the recognition of the benefits of cooperation and the sharing of critical technologies. Despite the governmental withdrawal of Germany, some German and Italian companies maintained their involvement in component manufacturing, such as Aeritalia producing the left-hand wing assembly. The EAP’s very existence as a demonstrator for a European combat aircraft and the continued technical contributions from international partners underscored its role in fostering cross-border aerospace ties. The EAP effectively demonstrated the feasibility of these advanced technologies and the effectiveness of the collaborative development model, which was instrumental in maintaining broader European interest and commitment that fully materialized in the Eurofighter program.2. Historical Development and Program Overview
2.1 Origins and Collaborative Efforts
The conceptual framework for the EAP originated within the “Agile Combat Aircraft (ACA)” initiative, which began in the late 1970s and early 1980s. This program emerged as a strategic response to the perceived need for a new generation of combat aircraft in Western Europe. Initially, it was a collaborative endeavor spearheaded by British Aerospace (BAe), working in conjunction with Messerschmitt-Bölkow-Blohm (MBB) from West Germany and Aeritalia from Italy. This multinational approach aimed to pool resources and expertise for a complex undertaking, focusing on developing advanced technologies such as full-authority digital fly-by-wire controls and innovative manufacturing processes, which were deemed essential for the next generation of highly capable fighter aircraft. To generate interest and demonstrate progress, a full-scale mockup of the ACA was showcased at the 1982 Farnborough Airshow and subsequently at the 1983 Paris Air Show. It was at the 1983 Paris Air Show that the official launch of the Experimental Aircraft Programme (EAP) was announced, with the ambitious plan to manufacture and fly a pair of technology demonstrators to validate these cutting-edge concepts.2.2 Funding and Construction
The British Government made a significant financial commitment to the EAP. However, the multinational funding model faced challenges when West Germany ultimately decided not to provide its share of funding, leading to the cancellation of the planned second EAP airframe. Consequently, the program transitioned to being “exclusively funded by the UK,” drawing contributions from both the public sector (Ministry of Defence) and private aviation industry partners. Despite Germany’s governmental withdrawal, some German companies maintained their involvement, highlighting the strong technical ties established. This pivot in funding demonstrates a profound strategic commitment by British Aerospace and the UK government to maintain a leading edge in fighter aircraft development. The decision to proceed, adapting to geopolitical shifts while pushing technological boundaries, underscored BAe’s inherent technical capability and confidence to lead and execute such an advanced program largely independently, even while strategically leveraging international component manufacturing for specific parts. Construction of the sole EAP prototype, designated ZF534, commenced in the mid-1980s. The primary assembly took place at British Aerospace’s dedicated development facility, No. 2 Hangar, located in Warton, Lancashire. The airframe incorporated advanced materials and construction techniques: the front fuselage featured innovative structures made of Carbon-fiber-reinforced polymer composites and aluminium-lithium alloy. The center and rear fuselage sections, in contrast, utilized more conventional structures, partly a consequence of MBB’s withdrawal from full partnership. Component manufacturing was distributed among the remaining partners: the right-hand wing assembly, a co-bonded carbon fiber composite structure, was produced at BAe’s Samlesbury plant. The left-hand wing assembly was manufactured by Aeritalia in Turin, Italy. Carbon composite foreplanes were made at Preston/Samlesbury, and the windscreen and canopy assemblies were designed and manufactured by Aerostructures Hamble in Southampton.2.3 Key Milestones
The EAP program achieved several significant milestones throughout its operational life:- Rollout: The EAP was officially unveiled and rolled out at BAe’s Warton facility on April 18, 1986, in a ceremony attended by employees and Sir Raymond Lygo.
- Maiden Flight: The historic first flight occurred on August 8, 1986, piloted by test pilot Dave Eagles, who was BAe’s Executive Director of Flight Operations at the time. During this initial sortie, the aircraft reached Mach 1.1 at an altitude of 30,000 feet.
- Public Debut: Just three weeks after its maiden flight, in September 1986, the EAP made its public debut at the prestigious Farnborough Air Show, captivating audiences with its advanced design.
- Intensive Testing Phases: The EAP underwent an initial flight test program comprising 50 flights, which then expanded into a wider, more comprehensive testing regime. A significant achievement was its 100th flight, performed in June 1987 at the Paris Air Show, demonstrating a rapid pace of “100 flights in 10 months” for an experimental aircraft.
- Performance Achievements: Throughout its testing, the EAP consistently pushed performance envelopes, attaining a top speed of Mach 2.0 and demonstrating controlled flight at angles of attack exceeding 35 degrees, a capability considered “exceptional even by today’s standards”.
- Retirement: The EAP completed its 259th and final test sortie on May 1, 1991, having accumulated a total of 195.21 flying hours. By this point, the aircraft had successfully fulfilled its intended purpose as a critical development aid for future combat aircraft.
Date (Year, Month Day) | Event/Milestone | Descrição |
1983, May | Contract Signed | British Aerospace signs contract with British Government for EAP development. |
1983, May | Program Launch | Official launch of the Experimental Aircraft Programme (EAP) announced at Paris Air Show. |
1986, April 18 | Rollout | EAP officially unveiled at BAe Warton facility. |
1986, August 8 | Maiden Flight | First flight by Dave Eagles; reached Mach 1.1 at 30,000 ft. |
1986, September | Public Debut | EAP displayed at Farnborough Air Show. |
1987, June | 100th Flight | EAP performs its 100th flight at Paris Air Show, achieving 100 flights in 10 months. |
1987, December | Test Phase 3 | Increased focus on Eurofighter Typhoon technologies, including direct voice input and multi-function displays. |
1991, May 1 | Final Test Sortie | EAP completes its 259th and final test flight, accumulating 195.21 flying hours. |
2012, March 26 | Departure from Loughborough | EAP leaves Loughborough University for RAF Museum Cosford. |
2013, November | Public Display | Reconstituted EAP placed on public display at RAF Museum Cosford. |
2014, February | Official Donation | BAE Systems officially donates the EAP airframe to the RAF Museum Cosford. |
3. Revolutionary Design and Aerodynamic Profile
3.1 Core Design Philosophy
The EAP’s design was revolutionary, fundamentally centered on the concept of an “unstable aircraft from first flight”. This inherent aerodynamic instability was a deliberate design choice, specifically implemented to achieve “more agile” flight characteristics. This instability, while enhancing maneuverability, necessitated and drove the development of highly sophisticated “digital control” systems, allowing for precise management of the aircraft’s flight envelope. A fundamental objective of the EAP was to “evaluate the characteristics of an unstable aircraft and the merits of flight control systems and delta canards at speeds of up to Mach 2”. This experimental focus underscored its role as a testbed for advanced aerodynamic principles. The deliberate design of the EAP as an “unstable” aircraft, intended to achieve “greater agility”, represents a critical design philosophy shift. This inherent instability, while granting superior maneuverability, renders the aircraft impossible to fly manually without continuous, rapid adjustments. This necessitated and directly accelerated the development of a highly sophisticated, rapid-response “fly-by-wire” system, with “Flight Control Computers (FCCs)” that “had to work three times as fast as contemporary aircraft”. This demonstrates a fundamental causal relationship: the pursuit of extreme aerodynamic performance through instability directly mandated and accelerated the development of equally extreme computational and control system capabilities. The EAP served as the crucial testbed for proving that this symbiotic relationship between aerodynamic design and digital control could be safely and effectively managed, thereby establishing a foundational principle for all subsequent agile combat aircraft designs.3.2 Airframe and Material Innovations
The EAP was a pioneer in the extensive use of advanced composite materials. Its wings were constructed from “carbon fibre,” a material choice that was “cutting edge” and “had never been done before” in such an application at the time. This provided significant advantages in terms of strength-to-weight ratio and potential aerodynamic performance. The front fuselage incorporated “innovative structures in Carbon-fiber-reinforced polymer composites and aluminium-lithium alloy”, showcasing a commitment to lightweight yet robust construction. The manufacturing process itself was innovative. The right-hand wing assembly was a “co-bonded carbon fibre composite assembly” produced at BAe’s Samlesbury plant, which “proved new tooling and manufacturing techniques” that were directly transferred and “put to good use later on the Eurofighter programme”. This indicates that the EAP was instrumental in pioneering and validating the industrial production processes required to fabricate complex, high-performance structures from these novel materials on a larger, more efficient scale. This was a significant hurdle for the subsequent Eurofighter program, making the EAP not just a design demonstrator but a vital manufacturing process demonstrator. A sophisticated design feature, similar to the Grumman X-29, was the “aero-elastically tailored” wings, engineered to prevent undesirable deformation under extreme aerodynamic pressures during high-performance maneuvers.3.3 Aerodynamic Features
The aircraft’s distinctive profile featured a “sleek delta-wing shape paired with forward canards,” a configuration known to significantly enhance maneuverability and aerodynamic performance, especially at high angles of attack. The large rear delta wings were specifically “cranked for high lift”. To minimize drag at supersonic speeds, the EAP incorporated an “area rule fuselage”. The aircraft utilized a “radome nose” and a “modified Panavia Tornado fin”. The use of a Tornado fin was a pragmatic decision to reduce costs and leverage existing components where the primary research focus was elsewhere. Control surfaces were highly advanced: “full-span trailing edge flaps” managed roll and pitch control, while “leading edge flaps” could be “electronically manipulated by a flight control system” to dynamically optimize wing camber and maximize maneuverability across various flight conditions. The EAP’s general characteristics and dimensions are detailed as follows:- Crew: 1
- Length: 14.7003 m (48 ft 2.75 in)
- Wingspan: 11.76 m (38 ft 7 in)
- Height: 5.525 m (18 ft 1.5 in)
- Wing area: 52 m² (560 sq ft)
- Empty weight: 10,002 kg (22,050 lb)
- Max takeoff weight: 14,515 kg (32,000 lb)
4. Cutting-Edge Technological Systems
4.1 Advanced Flight Control Systems
A defining innovation of the EAP was its “fly-by-wire controls,” characterized by the complete absence of mechanical rods connecting the control sticks to the flight control surfaces. Instead, pilot inputs were translated into electronic signals, enabling unprecedented “greater precision and responsiveness,” particularly vital for an inherently unstable design. The EAP’s inherent aerodynamic instability demanded exceptionally fast processing from its Flight Control Computers (FCCs), which were required to operate “three times as fast as contemporary aircraft” to maintain stable flight. This requirement highlighted the critical need for robust and high-speed computational power to manage the complex dynamics of an agile, unstable platform. To enhance safety during extreme maneuvers, the system incorporated a “departure prevention system” designed to automatically intervene at high angles of attack, preventing uncontrolled flight conditions. Throughout the flight test program, the EAP’s control laws were continuously refined. This included the implementation of advanced “Paris Standard” control laws, which incorporated crucial angle-of-attack and side-slip feedback to optimize handling across the flight envelope. A critical incident in September 1986, where a computer failure caused all cockpit displays to go down, demonstrated the robustness of the EAP’s safety protocols, as the aircraft was successfully returned to base using backup instrumentation. This event, while challenging, provided invaluable data on system redundancy and pilot response under extreme conditions, directly contributing to the safety and reliability standards for future combat aircraft.4.2 Avionics and Cockpit Integration
The EAP was equipped with a comprehensive suite of “advanced electronic equipment”, reflecting its role as a testbed for future combat aircraft avionics. The cockpit featured “three cathode-ray tube (CRT) displays” and a “Head-up display (HUD)”, providing pilots with critical flight and systems information. The HUD was noted as being similar to that found in the American General Dynamics F-16 Fighting Falcon. Flight controls were designed to be “Hands On Throttle-And-Stick (HOTAS)-compatible,” a crucial ergonomic feature allowing pilots to manage critical functions (such as weapon selection and sensor modes) without removing their hands from the primary flight controls. A particularly impressive and pioneering system was the “Utility Services Management System (USMS).” This advanced system linked over 600 different input and output signals from electronically controlled devices located throughout the aircraft. The USMS regulated diverse functions, including hydraulic systems control, anti-skidding, cockpit temperature monitoring, and secondary power system control, demonstrating a high level of digital integration. This detailed description of the USMS managing such a vast array of disparate, critical functions reveals a highly advanced level of systems integration. This goes beyond the mere presence of individual advanced components (like fly-by-wire or composite structures) to demonstrate the EAP’s pioneering role in how these disparate systems could be digitally networked, centrally controlled, and monitored within a single, high-performance platform. This holistic approach to aircraft design, where electronics and software are central to virtually every aspect of the aircraft’s operation, was revolutionary for its time and directly informed the integrated architecture of the Eurofighter Typhoon. Later phases of the test program, commencing in December 1987, specifically focused on evaluating technologies destined for the Eurofighter Typhoon, such as “direct voice input and multi-function displays,” pushing the boundaries of pilot-aircraft interaction. The cockpit design was a collaborative effort, described as a “pilot’s cockpit, designed by pilots, for pilots,” with Chris Yeo involved in its development. This emphasis on human-centered design was critical for optimizing the interface in such a complex and agile aircraft, ensuring that the advanced technology could be effectively utilized by the pilot.4.3 Propulsion System
The EAP was powered by a pair of “Turbo-Union RB199-104 afterburning turbofans”. These engines were a proven choice, having previously served as the powerplant for the Panavia Tornado ADV, indicating a pragmatic approach to leveraging existing, reliable technology for non-experimental subsystems where the primary research focus was elsewhere. Each RB199-104D engine delivered a substantial thrust of 40 kN (9,000 lbf) in dry thrust mode and 76 kN (17,000 lbf) with afterburner engaged, providing ample power for supersonic flight and high-agility maneuvers. In a further effort to reduce costs and streamline development, parts of the rear fuselage and the tailfin of a Panavia Tornado were adapted and utilized for the EAP prototype. As a pure experimental aircraft, the EAP was not equipped with operational armaments or military systems. However, dummy munitions were sometimes fitted for aerodynamic testing and to evaluate their impact on flight characteristics. The radome, typically housing radar, was instead used for flight test instrumentation.5. Performance Specifications and Flight Test Program
The British Aerospace EAP was designed to push the boundaries of flight performance, serving as a critical testbed for advanced aerodynamic and control concepts. Its performance specifications reflect its role as a high-speed, highly agile demonstrator:- Maximum Speed: The aircraft was capable of reaching speeds in excess of Mach 2.0. Test pilot Dave Eagles achieved Mach 1.1 at 30,000 feet during its maiden flight on August 8, 1986, with later trials confirming its Mach 2.0 capability.
- Service Ceiling: The EAP had a service ceiling of 60,000 ft (18,000 m), demonstrating its ability to operate at high altitudes relevant for future combat engagements.
- Angle of Attack Capability: A notable achievement was its ability to fly at angles of attack exceeding 35 degrees in controlled flight. This capability was considered “exceptional even by today’s standards”, showcasing the effectiveness of its unstable design coupled with advanced flight control systems in achieving extreme maneuverability.
- Electromagnetic compatibility tests: These were vital for ensuring that the aircraft’s complex electronic systems could operate without interference from each other or external sources, a critical aspect for modern combat aircraft.
- Validation of flight-control systems: This involved rigorous testing and refinement of the advanced fly-by-wire system, especially critical given the aircraft’s inherent instability. The continuous refinement of control laws, including the “Paris Standard,” allowed the EAP to push its flight envelope safely.
- Avionics and radar signature investigations: Research into the aircraft’s electronic systems and its radar cross-section was conducted at the BAe Warton radar cross-section range. This provided crucial data for stealth and combat effectiveness considerations for future designs.
6. Legacy and Influence on the Eurofighter Typhoon
The British Aerospace EAP’s most profound and enduring legacy lies in its direct and indispensable role in the development of the Eurofighter Typhoon. The EAP was not merely a conceptual exercise; it was explicitly described as “the technology demonstrator which ‘gave birth’ to the technology behind our Typhoon jet”. This statement underscores a direct lineage, where the EAP served as the foundational precursor, demonstrating and refining the advanced technologies that would become integral to the Typhoon’s design and capabilities. The EAP was specifically used for flight testing a variety of technologies that would later be incorporated into the Typhoon. These included critical areas such as electromagnetic compatibility tests, the validation and refinement of flight-control systems, and extensive avionics and radar signature investigations conducted at the BAe Warton radar cross-section range. The EAP’s trials pushed performance boundaries, such as flying at angles of attack exceeding 35 degrees, which was exceptional even by later standards. These demonstrations provided concrete evidence of the feasibility and effectiveness of these advanced concepts, directly informing the design choices for the Eurofighter. Chris Boardman, a managing director at BAE Systems, commented in 2013 that the EAP was “fundamentally important to defining and developing both the characteristics and capabilities of the subsequent Eurofighter Typhoon”. This assessment is supported by the British House of Commons Accounts Committee, which credited the EAP with reducing the Eurofighter’s development by a year, resulting in a substantial saving of £850 million. This quantifiable impact highlights the EAP’s strategic value as a risk-reduction and efficiency-enhancing program. The EAP’s success in proving advanced manufacturing techniques, such as the co-bonded carbon fiber composite assembly for the right-hand wing, directly translated into new tooling and manufacturing processes “put to good use later on the Eurofighter programme”. This indicates that the EAP was not just validating design concepts but also pioneering the industrial processes necessary for their large-scale production, a significant contribution to the Eurofighter’s manufacturability. The EAP’s rigorous flight testing also contributed heavily to the development of computerized flight control systems, new construction techniques, and the exploration of advanced aerodynamics. The lessons learned from managing the EAP’s inherent instability with its fast-acting fly-by-wire system were directly applicable to the Eurofighter, which also utilizes an unstable aerodynamic design for agility. Dave Ward, a member of the BAE Systems Flight Test Operations team involved in the program, aptly described the EAP as building “an aircraft for the future” and the “forefather of the next generation of flight”. This sentiment captures the profound influence the EAP had, shaping not just the Eurofighter but also setting new standards for the design and development of subsequent high-performance combat aircraft globally.7. Current Status and Preservation
Upon the conclusion of its flight test program on May 1, 1991, the British Aerospace EAP aircraft was retired from active service. Following its retirement, the EAP was initially stored at Warton before being transported to the Department of Aeronautical, Automotive Engineering and Transport Studies at Loughborough University, Leicestershire. For over a decade, from 1996 to 2012, it served as an invaluable instructional aid for undergraduate students studying Aeronautical Engineering. Its presence allowed students to carry out design appreciation exercises and gain practical understanding of the components and systems of a modern fighter jet. To facilitate this educational purpose, its port wing had been removed at the root, providing a clearer view of both the aerofoil cross-section and several internal components. Several other components were also removed for viewing. In March 2012, the EAP departed Loughborough University following a request from the Royal Air Force (RAF) to have it displayed at the Royal Air Force Museum Cosford, located in Shropshire. As compensation for the EAP’s departure, Loughborough University’s Aeronautical and Automotive Engineering department received a BAE Hawk 200 to replace it as a teaching and research aid. The airframe of the EAP arrived at the RAF Museum Cosford in 2012. In February 2014, BAE Systems officially donated the airframe to the museum. Following limited restoration work, the reconstituted EAP was placed on public display in November 2013. It now forms the centerpiece of a new exhibition featuring the groundbreaking achievements of the aircraft, sitting alongside previously unseen video footage, interactive kiosks, and images. Members of the public can visit the museum’s ‘Test Flight’ hangar to view the exhibition, which has been funded by BAE Systems. The EAP, registered as ZF534, is currently a prominent exhibit at the RAF Museum Cosford, serving as a tangible link to the technological advancements that led to the Eurofighter Typhoon.8. Conclusion
The British Aerospace Experimental Aircraft Programme (EAP) stands as a monumental achievement in aerospace engineering, representing a pivotal bridge between conventional aircraft design and the advanced combat aircraft of today. Conceived as a strategic technology demonstrator, the EAP’s primary purpose was to validate pioneering concepts for a future European fighter, a role it fulfilled with exceptional success. Its revolutionary design, characterized by inherent aerodynamic instability, necessitated and drove the development of highly sophisticated fly-by-wire flight control systems, whose rapid processing capabilities were unprecedented for the era. The extensive and innovative use of advanced materials, particularly carbon-fiber composites, not only pushed the boundaries of aircraft construction but also proved vital new manufacturing techniques that were directly transferred to the Eurofighter Typhoon program. This demonstrated the EAP’s contribution not just to design validation but to industrial production readiness. Through a meticulously planned and aggressively executed flight test program, the EAP systematically explored and validated critical technologies in aerodynamics, avionics, and structural integrity. Its ability to achieve Mach 2.0 speeds and maintain controlled flight at extreme angles of attack, even with its inherent instability, showcased the profound synergy between its radical design and its advanced digital control systems. This interdependence was a key learning from the program, establishing a foundational principle for subsequent agile combat aircraft. The EAP’s legacy is most tangibly realized in the Eurofighter Typhoon. It served as the direct “forefather” and “gave birth” to the core technologies that define the Typhoon’s characteristics and capabilities, including its flight control laws, avionics architecture, and manufacturing processes. The EAP’s efforts significantly de-risked the Typhoon program, leading to substantial savings in development time and cost. Today, preserved at the RAF Museum Cosford, the EAP continues to serve an educational purpose, embodying the spirit of innovation and the rigorous scientific inquiry that propelled aerospace technology into a new era. It remains a powerful symbol of British aerospace ingenuity and a testament to the strategic value of dedicated technology demonstrators in shaping the future of aviation.Vistas : 24